Leanna Wierzba, co-curator of the Fashion Space Gallery, tells us why 3D printing might spell the end of disposable high street fashion.
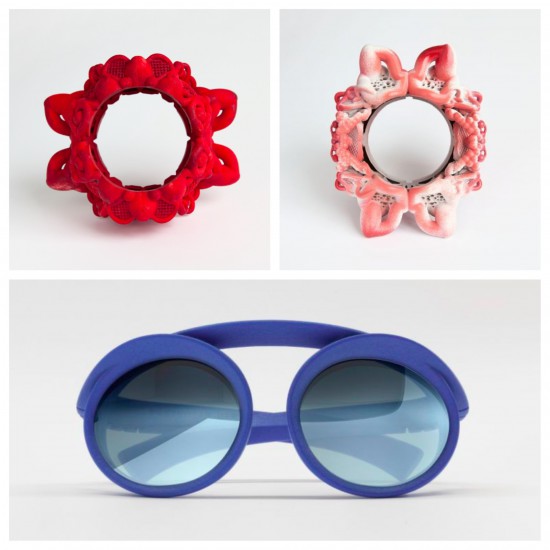
Hands up anybody who thinks that 3D printing is, well, kind of magic. We’re still baffled when the office printer gets a paper jam – so the idea of hitting ‘print’ on a new pair of Louboutins seems nothing short of miraculous.
This is where Layer By Layer steps in. The new exhibition at Fashion Space Gallery in London College of Fashion seeks to demystify the digital technology and demonstrates how fashion designers have utilised it in their work.
As co-curator Leanna Wierzba notes, “Designers using 3D printing are really trailblazers. Many of the pieces in the exhibition have been developed as prototypes and very few are wearable.”
The process itself isn’t actually that difficult to grasp. Desktop printers like the Makerbot (one is on show at the gallery) have an open-frame design, which allows viewers to see an object being successively printed out in thin layers of plastic. The result? An astonishing array of design objects – from the skull-inspired Biomimicry shoes by Marieka Ratsma and Kostika Spaho to the graceful curves of Ron Arad’s pq eyewear.
Wierzba believes that 3D printing will eventually offer an excellent alternative to fast, disposable fashion. “Instead of speculatively producing huge quantities of items at a very real cost to the environment, items can be made on demand and adapted easily to suite a new trend,” she enthuses. “A system like iTunes will probably be developed, whereby a user is able to access a file to print for a limited time or quantity.”
She points to design companies like Nervous System, who already make 3D printed jewellery to demand. “A customer can customise their own jewellery from one of their collections on the website using a special app,” Wierzba explains. “Each object is then printed out individually based on these specifications. Because their jewellery is not factory manufactured in mass quantities or crafted by hand, it’s sustainable and reasonably affordable.”
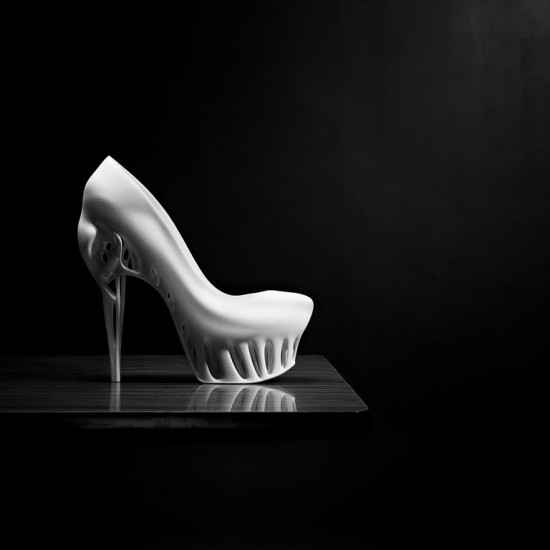
For those who fancy a go on their own, there’s already a huge market for 3D home printers, which can be purchased for under £2000 (already cheaper than when the first desktop printer was introduced ). Sites like Thingiverse already sell files that let users create anything from iPhone covers to toy helicopters.
“It’s already completely possible – and inexpensive – to print a variety of different objects at home,” Wierzba says. “There are currently a lot of free 3D files available online, created by people for the joy of exploring this medium.”
Hold your horses, though – while you can print on materials like ceramic, nylon, wax and titanium and readily apply the final product to jewellery or shoes, it’s much tougher to print on fabric (Wierzba doesn’t rule that out in the near future, with the development of new multi-material printers that can use both hard and soft materials).
And you won’t get away with printing a rip-off Burberry handbag anytime soon, either. “There’s a lot of work being done to develop a methodology for copywriting 3D designs – larger brands and serious designers will create clever ways of protecting their work,” Wierza says. “But it is incredibly hard to predict how and how fast this technology will develop.”
Even if we’re a long way off printing next season Céline, Layer By Layer is a must for anybody interested in fashion’s next incarnation – it’s an intriguing glimpse into the future of the industry. An iTunes directory of clothes? Custom-made app fashion? Photopolymer shoes? Beam us up.
Layer by Layer at the Fashion Space Gallery, London College of Fashion is curated by Leanne Wierzba and Gemma Williams. The exhibition will run from 10th April to 18th May. www.fashionspacegallery.com